Effective inventory management, best practices !
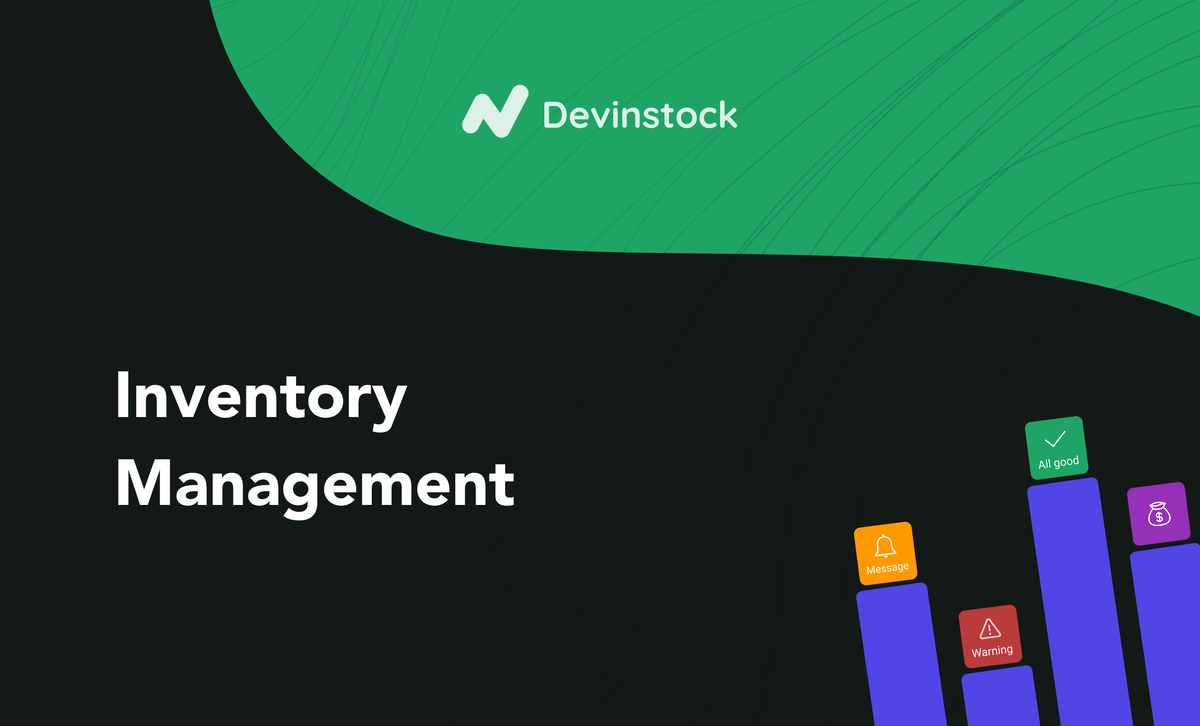
Product inventory management is a business process that involves overseeing and controlling a company's inventory of products or goods. It's an essential aspect of distribution and supply chain management for businesses that deal with physical products.
Ensuring to have an effective inventory management helps businesses to provision the right products in the right quantities at the right time, in order to minimize costs and maximize sales and benefits.
Key aspects of effective product inventory management
- Track: Monitoring the quantity, warehouse, and status of all products in stock.
- Forecast: Predict the future demand to maintain economic inventory levels.
- Ordering: Know when and how much to order to feed the stock.
- Storage: Efficiently organize and store products in warehouses or facilities.
- Stock valuation: Calculate the financial value of inventory for accounting purposes.
- Quality Control: Ensure products meet quality standards and manage products expiry dates.
- Reporting: Inventory analysis and reports for decision-making.
- Stock optimization: Balancing stock levels to avoid over stocks or stock outs.
- Multi-channel: Coordinate inventory across multiple sales channels (e.g., in-store, online, POS).
- Inventory management software: accelerate scan and track using barcode systems or RFID technology.
- Adjustments: Adapting inventory levels for seasonal fluctuations in demand.
- Manage product returns: Managing product returns and recalls efficiently.
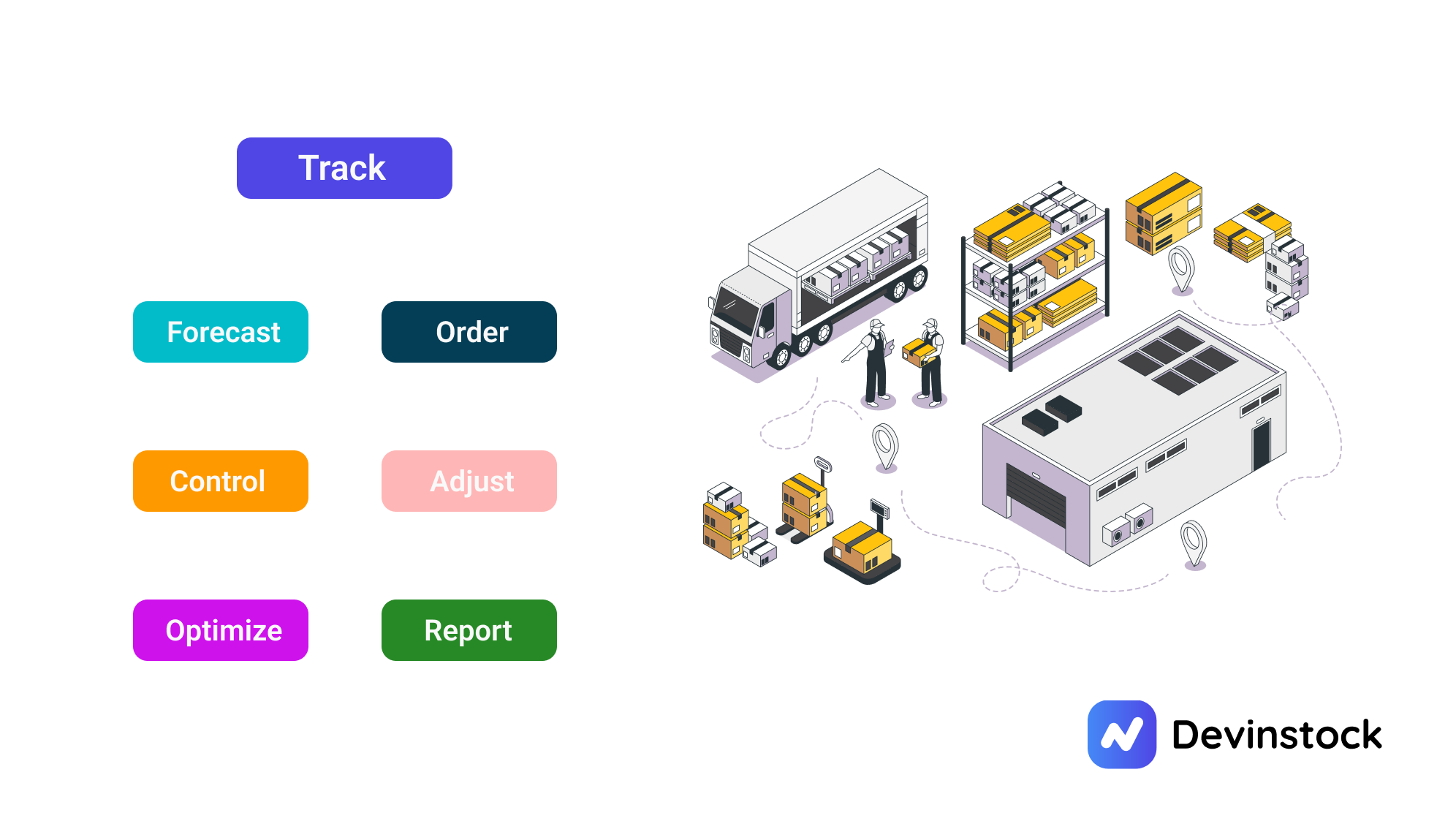
Why should you adopt effective inventory management ?
Effective inventory management impacts your customer satisfaction, operational efficiency, and company profitability. Adopting it can:
- Reduce costs associated with holding excess inventory.
- Prevent stockouts that could lead to lost sales opportunities.
- Improve cash flow by optimizing inventory investment.
- Enhance customer satisfaction through product availability.
- Identify best items, slow-moving or obsolete ones
What are product inventory tracking methods ?
Products inventory tracking methods are various approaches businesses use to track, manage, and control a product inventory. 3 commons methods are, basic tracking, batch tracking and serial number tracking. Let's explore these methods with examples from different industries:
Basic Tracking
Basic tracking involves no criteria when selecting products; items are chosen without considering any specific parameters while performing stock in and out transactions.
Batch Tracking
Batch tracking involves grouping inventory items that are produced together often with the same conditions and assigned with a unique batch number (Ex: batch #2812344). This method helps in tracking products from production to sale, ensuring quality control and tracking.
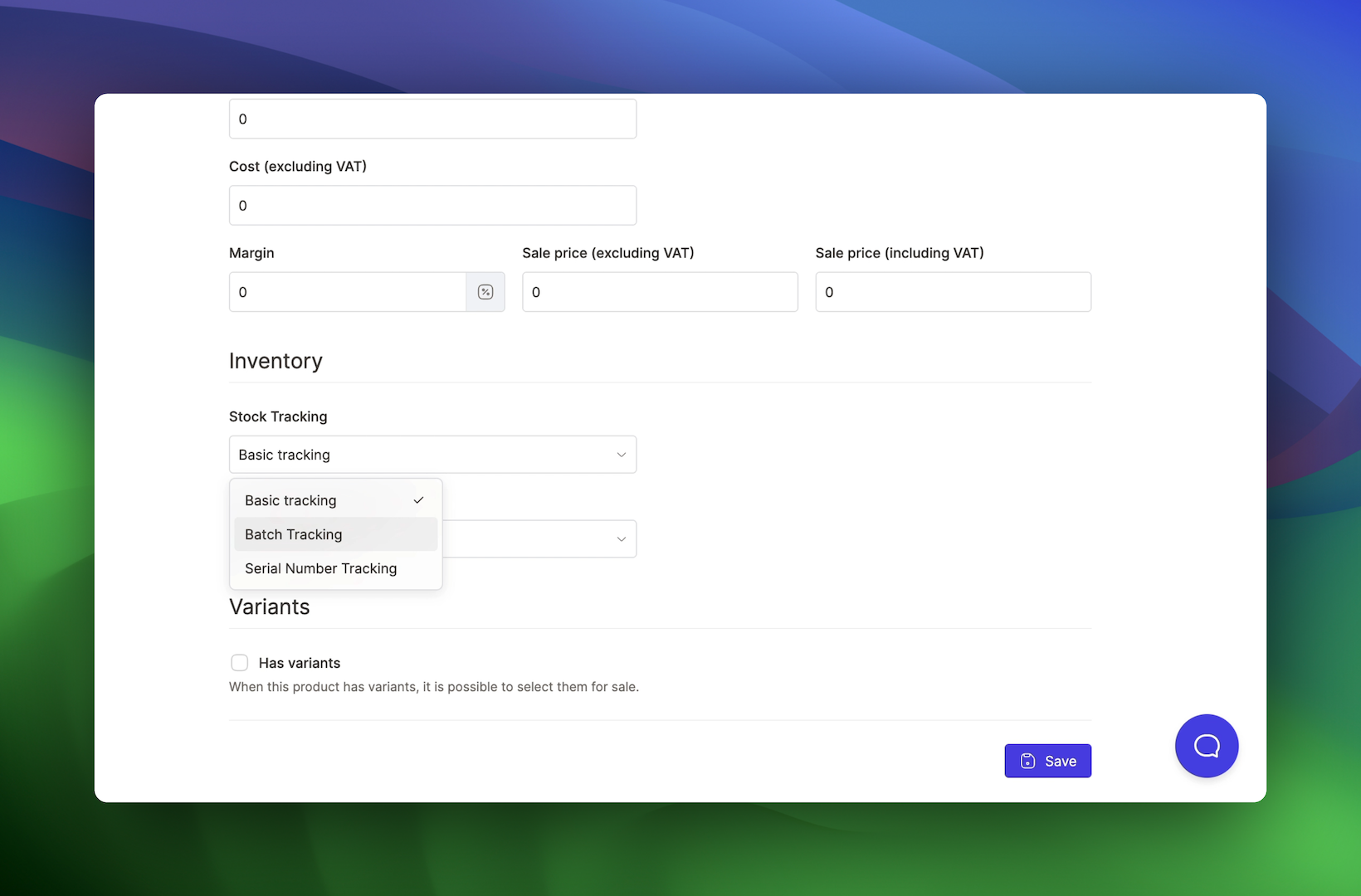
Example 1: Food Company
A yogurt manufacturer uses batch tracking:
- Each batch of yogurts produced in a specific date is assigned a unique batch number.
- This allows tracking of ingredients used, production date, and expiration date.
- If there's a quality issue, the company can quickly identify all products from the affected batch.
Example 2: Pharmaceutical Company
Medicines produced in one production run are assigned a batch number.
- This helps in tracking expiration dates and ensuring quality control across batches.
Example 3: Automobile Parts Company:
An automobile equipments parts manufacturer produces brake pads in batches. Each batch is tested for quality, and if a defect is found in a particular batch (Batch #0123), the manufacturer can recall only the defective batch rather than all brake pads in inventory, saving costs and maintaining safety
Serial Number Tracking
Serial number tracking involves assigning a unique identifier to each individual product. This method provides precise tracking and is essential for high-value or complex items.
Example 1: Automobile parts equipments
- Each engine part is given a unique serial number.
- This allows tracking of which specific part went into which vehicle.
- Useful for warranty claims, recalls, and quality control.
Example 2: Electronics manufacturer
- Every smartphone produced is assigned a unique serial number.
- Helps in tracking warranty information, service history, and ownership.
Example 3: Automotive Industry
- Car tires might use batch tracking for production runs.
- The entire vehicle itself is then assigned a unique Vehicle Identification Number (VIN), which is a form of serial tracking.
What are stock management methods ?
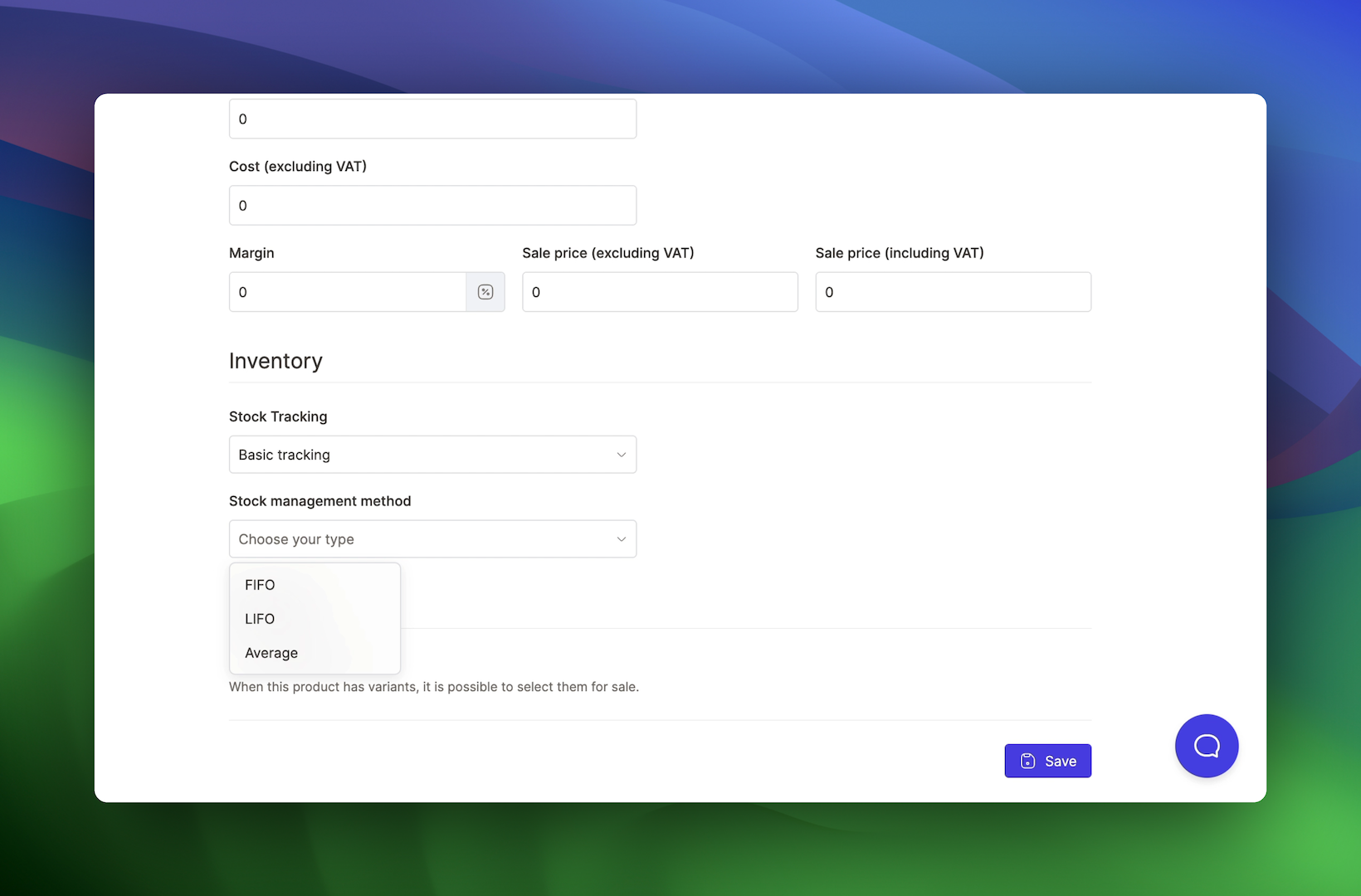
Products inventory management methods are approaches businesses use to value the stock and the item ins and outs. Each of these methods serves different purposes and choosing the right inventory method depends on various factors:
- Nature of the product (durable or perishable)
- Regulations: especially important in food and pharmaceuticals.
- Value of individual items.
- Volume of inventory.
- Need for traceability.
First In First Out
FIFO is an inventory valuation method where the oldest inventory items are sold first. This method is useful for goods that expires to ensure older items are used before they perish.
Example: Perishable Food Items
- A grocery store sells milk based on expiration dates, ensuring older stock is sold before newer stock.
Last In First Out
LIFO is an inventory valuation method where the most recently produced or purchased items are sold first. This method can be beneficial for tax purposes in certain jurisdictions but is less common in industries where inventory must be rotated regularly.
Ex: Construction Materials
- A hardware store might sell the most recently delivered lumber first, as it's often stacked on top and more easily accessible.
Just In Time
JIT is an inventory management method where materials and products are ordered and received only in time needed for projects, production or sales. This reduces holding inventory costs and minimizes products excesses.
- A fast-food chain uses JIT to manage its fresh products. Vegetables are ordered on a daily based on demand, it reduces waste and ensure fresh items.
ABC Method
ABC analysis is a method of categorizing inventory into three classes (A, B, and C) based on their importance and value. This helps in prioritizing inventory management operations efforts and optimize stock levels.
- "A" items are the most valuable.
- "B" items are less critical.
- "C" items are the least valuable.
A supermarket categorizes its inventory: 'A' items are high value products like meats, 'B' items are mid-range goods like dairy products, and 'C' items are low-cost, high-volume items like canned foods.
Perpetual Inventory System
Continuously updating inventory records as items are received or sold.
- A large Retail Chain Incorporate scanning products barcodes and usage POS systems to update inventory in real-time with each sale.
Manual Inventory System
Inventory is physically counted at specific intervals manually.
- A small boutique conducts a manual count of all items monthly to update inventory records.
Effective inventory management combining these methods helps in quality control, compliance, efficient recalls if needed, and overall distribution.
How the stock get impacted?
Stock impact refers to any operation that affects the quantity, value, or availability of inventory in a warehouse point. These impacts can be increasing or decreasing the stock levels. Managing impacts events data and details is important for maintaining inventory levels and ensuring smooth business operations.
Let's discover the operations that normally impact the stock:
Purchase reception: PR
- Stock Increases: When new inventory is received from suppliers, it will be validated by the business specialist, or warehouse manager. The stock impact operation will increase the stock level for the items added.
- Example: A retailer orders 100 units of a product, and upon reception, these units are added to the stock.
Sales delivery
- Stock decreases: When products are sold, they are substracted from inventory, reducing stock quantity.
Ex: A customer buys 5 units of a product from a store: These items units are deducted from the stock.
Manufacturing
- Raw materials decrease: In manufacturing, finished goods are composed of raw materials that are used to produce it, when a new production plan is validated, it will consume the stock of the raw materials. In other the hand, the production process increases the stock of finished goods.
Ex: A company uses glass, aluminum bars, and accessories to manufacture on-demand aluminum windows.
Elevate your inventory management with Devinstock 🚀
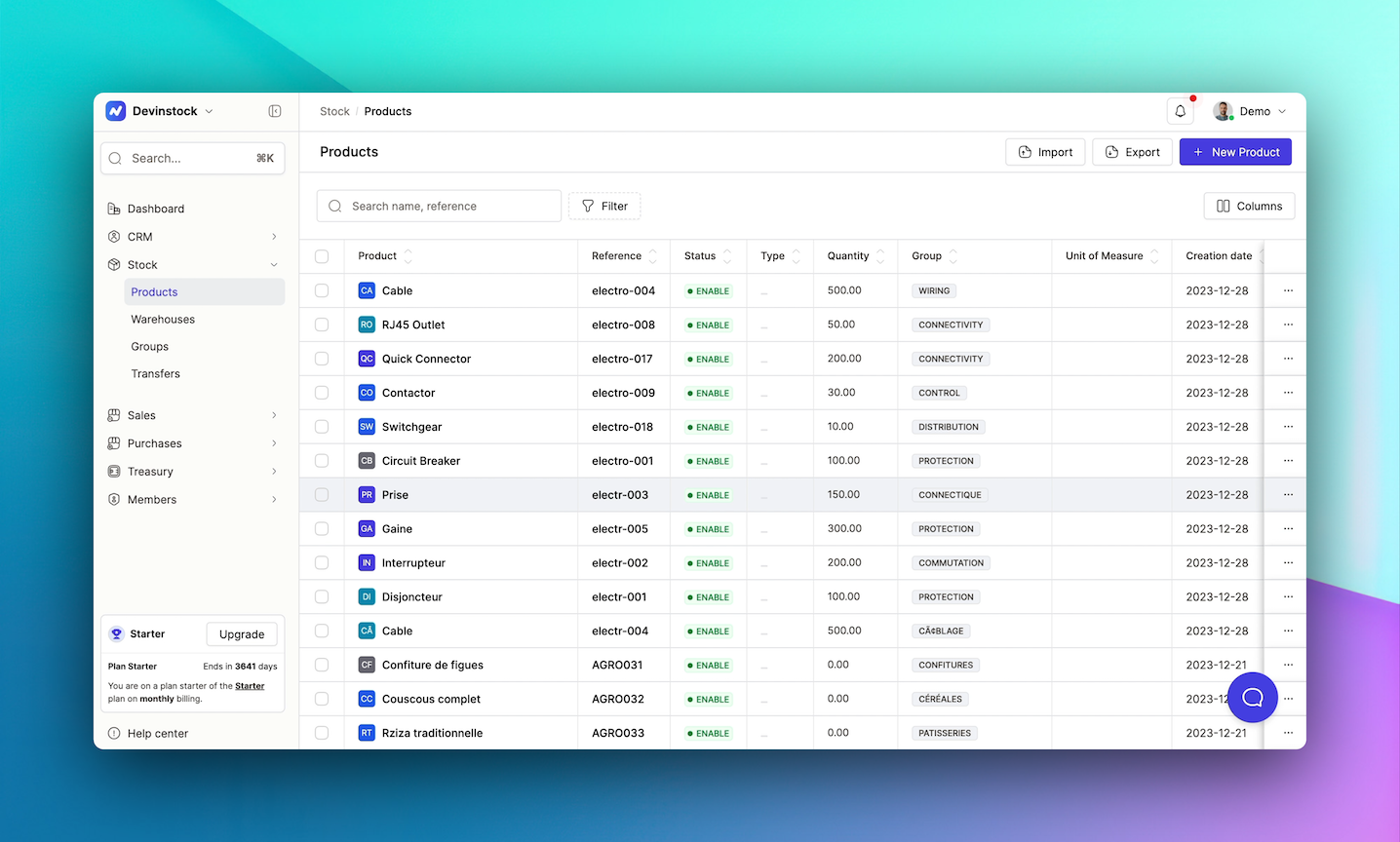
Adjustments (Manual)
- This operation is made to correct the differences found during inventory counts or audits reporting. These can be due to human errors, damage, expiry, or theft.
Stock Transfers
- It's when we move the stock between different locations, warehouses, or stores within the company. The total inventory remains the same, but stock levels at specific warehouse locations change.
Returns
- Customer Returns: When customers return products de the company, the returned items are added back to the stock: stock increases.
- Supplier Returns: When defective or sent by mistake item is returned to suppliers, it decreases stock levels
Damages and expiry
- Damaged items or expired products reduces stock levels when the products are written off from the inventory.
The ultimate tool for inventory professionals!
- 👨🏻💻 Collaborate with a dynamic team of innovative consultants.
- 🌍 Seamlessly integrated inventory tracking.
- 🖥️ Enjoy a unique and intuitive user experience.
- 📦 Effortlessly migrate your product data and accounts.
- 👥 Access a dedicated support team available 24/6.